ENGINEERING EXPERTISE
Proven track record in toolmaking and plastic injection moulding.
QUALITY ASSURANCE
ISO 9001 Certified: Guaranteeing high-quality products and processes.
CUSTOMER SATISFACTION
Ensuring your success through competitive pricing, on-time delivery, and transparent communication.
MULTI-SECTOR EXPERIENCE
Explore how our four decades of diverse industry experience can benefit you.
Streamline Costs and Efficiency from the Outset
Design for Manufacture (DFM) is the cornerstone of creating cost-effective products. By considering manufacturing capabilities and limitations during the design phase, DFM streamlines production reduces costs and ensures high-quality output.
Explore our DFM services to see how we can help optimise your designs for efficient and economical manufacturing.
During your initial consultation, we can review your designs and product specifications and offer advice on the following:
​
-
Material Selection: Guidance on choosing the most suitable polymers for your plastic parts.
-
Design Simplification: Advice on reducing complexity to improve manufacturability, including:
-
Runner and Gate Design: Optimise the design of runners and gates to reduce excess material usage—use hot runner systems to minimise waste by eliminating the need for runners.
-
Wall Thickness: Advice on ensuring uniform wall thickness to prevent issues like warping, sink marks, and uneven cooling.
-
Ribbing and Reinforcements: Advice on adding strength through ribbing and reinforcements without significantly increasing material usage.
-
Weight Reduction: Advice on reducing material usage and weight by hollowing out sections while maintaining structural integrity.
-
Draft Angles and Transitions: Advice on incorporating appropriate draft angles and smooth transitions to facilitate easy part removal from the mould.
-
Undercuts and Side Actions: Advice on minimising undercuts and the need for side actions to simplify mould design and reduce complexity.
-
-
Mould Flow Simulation: Use mould flow simulation software to predict how the plastic will fill the mould and identify potential issues with part geometry.
-
Prototyping: Arrange for prototypes to validate the design and make necessary adjustments before full-scale production.

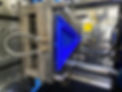
These services are designed to ensure that your products are optimised for efficient, high-quality, and cost-effective manufacturing from the very beginning.
​
Unlock the Potential of Design for Manufacture
with Paul Norman Plastics.
Contact us today to learn more about our DFM service and discover how we can help you streamline production of your plastic component parts.
​